Flute Grinding Wheels
Flute grinding wheels are specialized abrasive tools used in the manufacturing and reshaping of flute profiles on cutting tools such as end mills, drills, and reamers. These wheels are designed to precisely grind the flutes, or grooves, on the cutting tool to achieve the desired shape, dimensions, and surface finish.
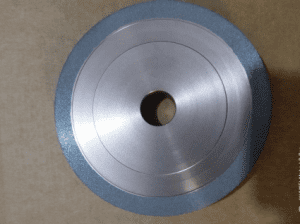
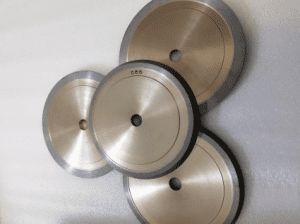
Here are some key features and considerations regarding flute grinding wheels:
Wheel Composition: Flute grinding wheels are typically made from abrasive materials such as diamond or cubic boron nitride (CBN). Diamond wheels are commonly used for grinding carbide cutting tools, while CBN wheels are suitable for grinding high-speed steel (HSS) cutting tools.
Wheel Bonding: The abrasive particles on the wheel are held together by a bonding material, which can be vitrified, resin, or metal. Vitrified bonds are often used for flute grinding wheels as they provide excellent cutting performance, dimensional stability, and thermal resistance.
Wheel Shape and Profiles: Flute grinding wheels come in various shapes and profiles to accommodate different flute designs. The wheel shape can be straight, cup-shaped, or dish-shaped, depending on the specific application and the desired flute profile.
Grit Size: The grit size of the abrasive particles on the wheel determines the surface finish and material removal rate. Coarser grit sizes are suitable for rapid material removal, while finer grit sizes provide a smoother finish.
Coolant Application: Grinding generates heat, which can affect the cutting tool and the grinding wheel itself. It is essential to use an appropriate coolant or lubricant during flute grinding to control the temperature and prevent thermal damage.
Dressing and Truing: Over time, the grinding wheel can wear and lose its shape. Dressing and truing processes are used to restore the wheel’s profile and remove any built-up debris or glazing on the wheel surface. Proper dressing and truing help maintain consistent flute geometry and grinding performance.
When selecting flute grinding wheels, it is crucial to consider factors such as the material of the cutting tool, desired flute profile, grinding requirements, and machine compatibility. It is recommended to consult with grinding wheel manufacturers or experts to determine the most suitable wheel specifications for your specific application.
Diamond grinding wheels |
Shape |
D |
T |
H |
X |
Grit |
Bond |
Body |
1A1 |
100 |
8 |
20 |
10 |
D54 |
Hybrid |
Copper |
1A1 |
100 |
10 |
20 |
10 |
D54 |
Hybrid |
Copper |
1A1 |
100 |
12 |
20 |
10 |
D54 |
Hybrid |
Copper |
1A1 |
100 |
15 |
20 |
10 |
D54 |
Hybrid |
Copper |
1A1 |
125 |
8 |
20 |
10 |
D54 |
Hybrid |
Copper |
1A1 |
125 |
10 |
20 |
10 |
D54 |
Hybrid |
Copper |
1A1 |
125 |
12 |
20 |
10 |
D54 |
Hybrid |
Copper |
1A1 |
125 |
15 |
20 |
10 |
D54 |
Hybrid |
Copper |
1A1 |
150 |
8 |
20 |
10 |
D54 |
Hybrid |
Copper |
1A1 |
150 |
10 |
20 |
10 |
D54 |
Hybrid |
Copper |
1A1 |
150 |
12 |
20 |
10 |
D54 |
Hybrid |
Copper |
1A1 |
150 |
15 |
20 |
10 |
D54 |
Hybrid |
Copper |